Applying four coats of varnish to the panels for the boot has kept me busy for a while, but having finished that it was time for something else.
There is no carpet for the rear of the boot bulkhead - so I decided to spray this black to cover up the patches of red gel-coat that showed through:
That's better.
Next job was to sort out the fuel tank sender. Now the consensus of the forums is that the GD supplied sender does not work as it does not suit the shape of the tank. But I had to think that if GD used it then it must work??
So I set about measuring / cutting / bending to get the sender arm to what I thought was the right shape. The next step was to test it....??
I did this by fixing the sender to the tank with duct tape and connecting the terminals to a multimeter to check the resistance of the sender to compare it against the min & max values obtained with the sender out of the tank. Firstly with the tank the right way up:
243 Ohms compared to 243 out of the tank. I then lengthened the float arm until the reading reduced from 243 (i.e. float touching the bottom of the tank) - this was about 5mm.
I then inverted the tank to check the "full" reading - this was a bit out so after a bit of arm adjusting and float bending to avoid the float fouling the tank front / baffle..... :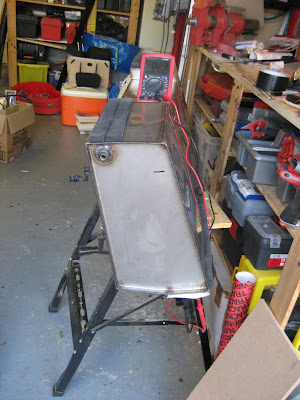
23 ohms compared to 23 out of the tank.
After a bit more faffing about and checking I'm pretty happy that the sender reads full when full and reads empty when the float is about 5mm off the bottom of the tank. This isn't empty empty as this still leaves the two siphon connected lower parts of the tank at each end - these are below two horizontal baffles which effectively act as the "floor" of the tank as far as the sender is concerned. This should leave a few litres of reserve - which at 10mpg should last a couple of minutes!!
The final job therefore was to solder up the two sections of the float arm at the determined optimum length:
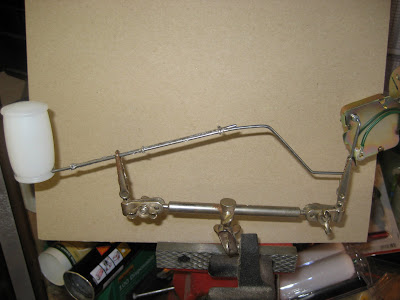
Now....
... where's my windscreen?