It is -2 degrees today and I've just spent the morning outside cleaning the wheels and polishing the rims and spinners - what a ball-ache it was with all the nooks and crannies on the Halibrands. Still it was much easier to do with the wheels off the car.
I went for the clear anodised finish on the rims and whilst it may not give the shiniest of shiny finishes it does seem to have protected them and made them easier to clean. The rims were finished off with the polish supplied by image with the wheels - which interestingly looks like, smells like, applies like and buffs off like Auto Glym Super Resin Polish!
I've put the back wheels back on(after making sure I had not forgotten to grease anything) but left the fronts off as I still need to check the front wheel bearings and callipers.
I'm too cold to be bothered to do anything else today!
Sunday 21 February 2010
Cleaning the Wheels
Posted by STR at 11:43 0 comments
Labels: Maintenance
Saturday 20 February 2010
Sat Nav...... In a Cobra????
Over the last few years I have become accustomed to using Sat Nav. And with the desire to travel abroad in the Cob - combined with my Wife's poor navigational skills I had been thinking about how to mount my Sat Nav in the Cobra. I had managed to conclude that the normal windscreen mounting brackets were not going to work and also that the unit needed to mounted low down to cut down on glare with having no roof. I hadn't really come up with a solution until I found a strip of spring steel in my oddments box.
I got a spare powered mount off E-bay and this was simply bolted to a hole drilled in the end of the arm:
The wires you keep seeing in the background are the leads from the battery conditioner you'll remember that I included a fly-lead under the dash to make connecting up easier.
Posted by STR at 16:15 1 comments
Labels: dashboard, Modifications and Upgrades
Sunday 14 February 2010
More Winter Jobs
Tme to crack on with my list of things to do. Worked over and under the entire car checking nuts and other fasteners and lubricating / greasing every thing that needed it. All fluids were present and correct:
Bit puzzling as the valve was screwd up F.T. when it was all assembled? - managed to nip it up another quarter turn so that should fettle things. Got a few more odds and sods to do but the main outstanding essential job is to fit the Hood and Sidescreens. These should be ready to collect in a couple of weeks - which will clash with going on holiday.
Posted by STR at 13:48 0 comments
Labels: Maintenance
Sunday 7 February 2010
Adjusting the Rev-Limiter
Following discussions with Jez my engine builder, he had informed me that it was OK to turn the Rev-Limiter up to 6000 rpm ( from the 5250 it is set at now). I was a bit worried that this would turn out to be a bit of a pain as I had hidden Mallory Hy-Fire unit away behind the dashboard - admittedly to put it out of the way of engine bay heat and water.
It was then a simple matter of unplugging the three harnesses and removing the heater vent pipe and Bob's your Uncle!Took the access panel off - twiddled the dial - and put it all back together - the under-dash panel went back as easily as it had come out.
Job Done.
Posted by STR at 14:38 0 comments
Labels: dashboard, Electrics, Engine, Modifications and Upgrades
Saturday 6 February 2010
Adjusting Wheel Cambers
First things first, a trip to Machine Mart kitted me out with a set of "wobble bars" - socket extensions that will accommodate a +/- 10 degree deviation in line:As you can see below - the 500mm bar is just the job:
With the four brake disc retaining nuts removed, 5 minutes of rotating the drive shaft and tapping with a rubber mallet saw the shaft come free allowing the shim pack to be adjusted:
With the correct shims fitted new disc retaining nuts were fitted (important not to use the old ones) and tightened to the correct torque. Conveniently you can use the handbrake to prevent the shaft rotating. This becomes a bit of pain when working on the nearside as you keep having to walk round the car to operate the handbrake.
Posted by STR at 14:25 0 comments
Labels: Front Suspension, Modifications and Upgrades, Rear Suspension
Jaguar Suspension Development
Before I get round to adjusting the wheel cambers on the car, it is time for a history lesson with some of the background behnd the Jaguar's development of its suspension systems:
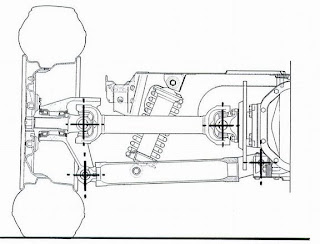
Posted by STR at 14:07 1 comments
Labels: Front Suspension, Rear Suspension